In the realm of radar technology, efficiency, precision, and reliability are paramount. Slip rings play an invaluable role in radar antennas, ensuring seamless performance while tackling challenges presented by demanding operational environments. This comprehensive article delves into the integration of slip rings in radar systems, covering everything from basic functions to expert insights and addressing common user concerns to facilitate informed decision-making.
Introduction Slip Ring Application in Radar Antenna
In the sophisticated world of radar technology, a seamless exchange of power and signals between stationary and rotating platforms is critical. This is particularly true for radar antenna systems, which must continuously rotate to detect objects in the air or at sea accurately. At the heart of this capability lies the unassuming but essential device known as the slip ring. Slip rings are engineered to provide a continuous electrical connection amidst the relentless motion, proving indispensable for reliable radar operations.
The centrality of slip rings in radar systems cannot be understated—they are the robust links that carry electrical currents, vital control signals, and data between the radar’s stationary infrastructure and its moving antenna. The unique makeup of slip rings allows for uninterrupted power supply and data transfer, which is pivotal in maintaining the radar’s operational integrity and responsiveness. In an environment where precision is non-negotiable, the slip ring stands as a sentinel, ensuring that despite the perpetual rotation of the antenna, there is no loss in the quality or speed of information relayed.
But slip rings are not one-size-fits-all; they must be tailored to the demands of each unique radar system. Features such as electrical noise reduction, minimal contact resistance, and longevity under considerable mechanical wear are just a few of the critical specifications that radar system designers consider. Additionally, these components must be crafted to withstand the often harsh environments in which radar systems operate—temperatures, vibration, and weather conditions that would compromise lesser components.
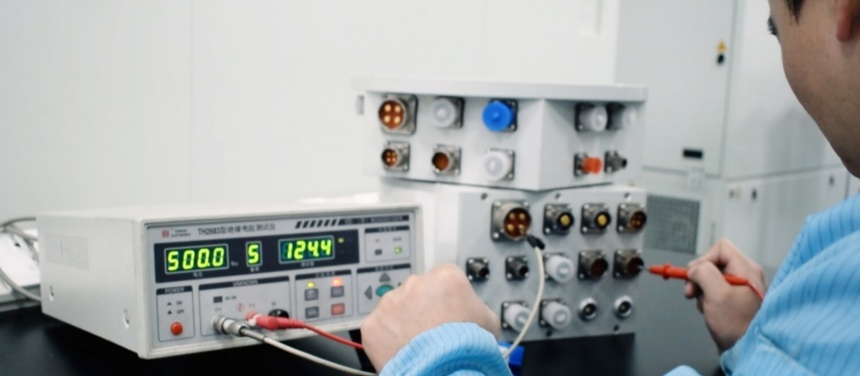
Understanding slip rings’ fundamental properties and characteristics is essential to appreciate their significant role fully. This introduction lays the groundwork for an exploration into how slip rings function within radar antenna systems and highlights the confluence of engineering and innovation that ensures these devices not only meet but exceed the multifaceted demands placed upon them. The following sections will delve deeper into the mechanics, the challenges, and the solutions presented by slip rings, illuminating their indispensable nature in the continuous evolution of radar technology.
Understanding Slip Rings and Their Role in Radar Antennas
To comprehend the functionality of slip rings and their significant role in radar antennas, we must first understand what they are. Slip rings, also known as rotary electrical interfaces, revolving connectors, or electrical rotary joints, are devices that provide an electrical connection between a stationary system and a part that rotates or moves. They do this while maintaining a constant, unbroken electrical connection that permits power, signal, and data to be transferred accurately and reliably even during continuous rotation or motion.
In the context of a radar antenna system, the antenna continuously rotates or oscillates to detect and track objects across a broad field. This rotation necessitates the need for a mechanism that allows non-stop communication between the stationary parts of the radar system and the moving antenna—this is where slip rings take center stage.
The slip ring, often unnoticed yet irreplaceable, mounts onto the rotating axis of the radar antenna. As the antenna moves in its quest to scan the skies or seas, the slip ring maintains the required electrical connections and allows for the unbroken transmission of power and data, regardless of antenna motion or speed. This ability is crucial because any interruption or delay in data transfer could potentially lead to inaccurate tracking or detection, undermining the purpose of a radar system.
The structure of a slip ring is ingeniously simple yet effective. It primarily consists of two parts: the rotor that turns with the rotating platform (in this case, the radar antenna), and the stationary part known as the stator. The rotor and stator typically have conductive rings and brushes, respectively, creating points of contact. As the rotor turns, the brushes maintain continuous contact with the rings, ensuring a steady flow of electrical current or signals from the stationary source to the rotating part.
When applied to radar antennas, slip rings become a key factor in ensuring the reliable functionality of the entire system. They guarantee constant connectivity, promoting smooth, precise, and reliable operations. Without the incorporation of this pivotal component, radar antennas would not achieve the continuous rotation necessary for their operation, consequently rendering them ineffective for their primary role—monitoring and tracking targets.
This section thus sets the foundation for exploring how slip rings function within radar antenna systems, highlighting their critical role in enabling dynamic operation, precision tracking, and high data integrity. In upcoming sections, we will delve into specific challenges associated with slip ring application in radar antennas, and how they unfailingly rise to meet these challenges.
Key Concerns in Applying Slip Rings to Radar Antennas
The integration of slip rings in radar antenna systems presents several concerns for users and designers that have a direct impact on the overall performance and efficiency of the radar system. The following four key considerations must be thoroughly addressed to ensure optimal functioning and sustained, reliable performance throughout the radar system’s lifespan:
- Reliability and Longevity: One of the primary concerns for users is the reliability of the slip ring, as any malfunction or failure can directly affect the radar system’s operational capabilities. Operational interruptions or degraded performance can impede the security, communication, or tracking efforts that the radar system serves. Therefore, high-quality slip rings designed to withstand extended periods of wear without compromising their performance are of the utmost importance. Longevity must not only be demonstrated in normal operating conditions but also during the most demanding scenarios the radar system may encounter.
- Data Integrity and Speed: The accurate and timely transmission of data is the lifeblood of an effective radar system, and it is the slip ring that preserves data integrity as the antenna spins relentlessly. Users demand that the slip rings maintain a consistently high quality of power, signal, and data transmission, as any degradation in signal quality or distortion can impact the radar system’s ability to interpret and respond to incoming data. As such, slip rings need to be carefully engineered with proper shielding and low signal noise to ensure consistent, high-speed data transmission for radar systems to function effectively.
- Environmental Resistance: Radar antennas can often be found in a vast range of environments, from arctic cold to unforgiving heat, and everything in between, exposing them to potentially harsh conditions. Consequently, slip rings must be designed to accommodate and resist these environmental factors. This can include protection against corrosion, moisture ingress, extreme temperatures, and even electromagnetic interference (EMI). The slip ring’s integrity and performance mustn’t be compromised by these environmental variables, ensuring the radar antenna operates at full efficiency in every scenario.
- Maintenance Requirements: Radar systems are strategic assets that cannot afford extended downtime. Users prefer slip rings that demand minimal maintenance to ensure that the radar systems remain operational without the need for constant intervention. Easy access to the slip ring components, simple servicing procedures, and reduced wear on the contact materials can contribute to a significantly lower maintenance burden, ultimately translating to shorter downtimes and improved overall reliability.
Recognizing these key concerns provides a roadmap for evaluating and selecting the most appropriate slip ring for a given radar antenna system. Addressing these challenges will focus on the critical factors that contribute to extended operational performance, ultimately creating a radar system that can dependably monitor, track, and analyze targets in the harshest environments and most demanding situations.
Case Studies of Slip Ring Applications in Radar Antennas
The efficacy of slip rings in radar antenna systems can be best understood through real-world case studies that demonstrate how different types and configurations of slip rings have effectively addressed user requirements and challenges. The following case studies provide insight into how innovative slip ring designs and features have successfully contributed to the performance of various radar systems:
Case Study 1: Air Traffic Control Radar System
A slip ring manufacturer developed a specific slip ring model to cater to the needs of air traffic control (ATC) radar systems. This customized slip ring integrated multiple data and signal channels, along with a fiber optic rotary joint (FORJ) to transmit high-speed data between the stationary and rotating components. The slip ring effectively ensured constant contact and minimized signal noise, resulting in reliable, accurate data transmission with minimal interference. Additionally, the slip ring boasted of low-maintenance requirements, enhancing overall system efficiency. This successful integration of slip ring technology played a vital role in allowing the ATC radar to maintain continuous surveillance, facilitating safe navigation for countless aircraft.
Case Study 2: Maritime Radar and Weather Monitoring
A leading workplace safety solution provider needed a slip ring solution for their maritime radar and weather monitoring systems, which were exposed to harsh environments, including saltwater corrosion and extreme temperatures. The manufacturer developed a custom slip ring offering IP-rated sealing to protect against moisture ingress, corrosive environments, and temperature fluctuations. The slip ring’s contact materials also sustained excellent performance even under continuous mechanical stress, ensuring long-lasting, reliable data transfer to cope with the extreme conditions faced by these maritime and meteorological radar systems.
Case Study 3: Military Surveillance and Early Warning Radars
A defense contractor required a slip ring solution for its cutting-edge military surveillance and early warning radar systems that demanded a rapid, uninterrupted flow of data while maintaining a high level of data integrity and security. The slip ring supplier devised a high-frequency slip ring with advanced EMI shielding to minimize signal crosstalk and ensure high-speed and secure data transmission. This design allowed the radar antennas to maintain constant rotation while guaranteeing clear and accurate data transmission critical in defense and early warning scenarios.
Case Study 4: Mobile Radar System for Disaster Management
A disaster management agency needed a slip ring for their mobile radar system designed to operate in various terrains and rapidly deploy in exigent circumstances. The manufacturer developed a lightweight and compact slip ring featuring a rugged design, allowing for secure mounting on various mobile platforms with limited space. Furthermore, this slip ring boasted efficient power and signal transmission to ensure proper functioning despite demanding operating conditions. This implementation demonstrated the slip ring’s adaptability and durability in meeting unique challenges presented by disaster management applications.
These case studies illustrate how bespoke slip ring applications cater to a variety of radar antennas and the unique challenges posed by specific industries or environments. The tailored features and designs have decisively addressed user concerns while providing reliable, seamless, and efficient performance in each context, demonstrating the significance and versatility of slip rings within the realm of radar technology.
Slip Ring Application in Radar Antenna: Expert Opinions and User Experiences
Gaining insight into the views and experiences of industry experts and users can provide a wealth of understanding about the benefits and challenges faced in applying slip rings to radar antenna systems. This section compiles expert opinions on new trends and advancements in slip ring technology, complemented by user testimonials to highlight the value and significance of slip rings in radar antenna applications.
Expert Opinion 1: Integration of Fiber Optic Rotary Joints for High-Speed Data Transmission
A leading expert in rotary transmission systems has observed the increasing integration of fiber optic rotary joints (FORJs) in slip rings to meet the surge in demand for high-speed data transmission. According to the expert, this trend reflects the growing need for real-time data processing and transmission in radar systems. Integrating FORJs with traditional slip rings offers high bandwidth capabilities and exceptional performance, even in the most demanding radar antenna applications.
Expert Opinion 2: Customized and Modular Designs for Adaptable Solutions
A renowned radar system engineer emphasizes the importance of customizable and modular slip ring designs in the rapidly evolving radar landscape. Customizable slip rings offer refined solutions tailored to specific application requirements, while modular designs provide the flexibility to modify or expand the configuration to accommodate emerging operational needs in diverse radar environments. For example, an ID 7-inch slip ring can be customized to meet the unique needs of radar systems, allowing for higher power transmission or more circuits for complex signal processing. The slip ring is designed to be flexible, offering the ability to adapt to changes in the system’s requirements, making it ideal for environments where expansion or modification is frequently needed. This combination of customization and modularity ensures that radar systems remain efficient and future-proof, even as technology and operational demands evolve.
User Testimonial 1: Air Traffic Surveillance System
An air traffic control supervisor noted the critical role that a high-reliability slip ring played in their surveillance radar system. The slip ring with integrated fiber optic communication channels enabled continuous, high-quality data transmission between the stationary system and the rotating antenna, contributing to the effective monitoring and guidance of aircraft during both routine operations and emergency scenarios.
User Testimonial 2: Shipborne Radar System for Naval Vessels
A naval officer highlighted their positive experience with a slip ring specially designed for shipborne radar systems. The slip ring’s rugged build and environmental resistance, coupled with low maintenance requirements, delivered smooth and reliable operation during extended ship deployment and exposure to harsh marine conditions. This helped maintain optimal radar performance in critical defense operations.
Expert Opinion 3: Electromagnetic Interference Shielding for Robust Signal Integrity
A research scientist specializing in electromagnetic interference (EMI) management discussed the significance of EMI shielding in slip ring designs for radar antenna applications. EMI shielding helps maintain the integrity of sensitive signals transmitted through a slip ring, reducing noise and interference, and ensuring the radar system’s ability to accurately process and respond to incoming data. The researcher predicts an increasing focus on advanced EMI shielding technologies within the slip ring industry.
User Testimonial 3: Ground-Based Meteorological Radar System
A meteorological station manager shared their experience with a slip ring installed in their weather radar system. The slip ring, built to withstand extreme temperatures, humidity, and heavy precipitation, exhibited impressive durability and reliability throughout its service life. The station manager commended the slip ring for its long-lasting performance and minimal maintenance, noting that it contributed significantly to the continuous and accurate monitoring of critical weather data.
Looking for high-quality slip rings? Complete the form below for more information.
These expert opinions and user experiences underline the value of slip rings in various radar antenna applications and the importance of continuing developments to keep pace with emerging trends and technologies. Furthermore, they showcase the successful augmentation of radar systems based on the incorporation of cutting-edge slip ring design and features tailored to address specific application challenges.
Slip Ring Application in Radar Antenna: Considerations for Choosing the Right Slip Ring
Choosing the right slip ring plays a crucial role in ensuring the efficiency and reliability of radar antenna systems. While slip ring selection primarily depends on the specific application, some general considerations can guide this process. Identifying the right slip ring requires a holistic understanding of several selection parameters, including electrical requirements, mechanical constraints, environmental conditions, data transmission needs, and maintenance requirements:
Electrical Requirements:
The electrical requirements primarily refer to the number of channels (conductors), voltage rating, and current capacity of the slip ring. These requirements must align with the electrical power and signal communication needs of the radar antenna system. For example, radar systems with high power and signal demands may require more specialized slip rings that can handle higher voltage ratings and current capacities.
Mechanical Constraints:
Mechanical constraints include the consideration of factors such as the space available for the slip ring, the rotating speed of the antenna, as well the physical connection requirements. The size and weight of the slip ring can directly influence the ease of installation and compatibility with the existing radar system. Furthermore, the slip ring’s rotational speed rating must be compatible with the antenna’s rotational dynamics to ensure smooth operational performance.
Environmental Conditions:
Understanding the environmental conditions in which the radar antenna operates is essential to selecting a slip ring with suitable protection. Protection necessities might include resistance against moisture, corrosion, heat, cold, and electromagnetic interference, among other factors. For instance, radar antennas deployed in marine or outdoor weather-tracking applications would require slip rings explicitly designed to withstand harsh environmental factors and provide reliable service throughout their lifespan.
Data Transmission Needs:
Data transmission needs are rooted in the requirement of the radar system to handle high-speed data and signal communications. Factors such as data transfer rate, signal integrity, and bandwidth specific to the radar system should be considered when choosing a slip ring. Special slip rings integrating technologies like fiber optic rotary joints may be necessary for systems demanding ultra-high-speed and high-fidelity data transmission.
Maintenance Requirements:
Maintenance needs refer to how frequently the slip ring should be serviced or replaced. Choosing a slip ring with a long service life and low maintenance can reduce operational costs and ensure minimal interruption to the radar system’s function. Therefore, selecting a slip ring with high durability and reliability ratings, easy access for servicing, and low-wear materials can lead to prolonged life, reduced downtime, and improved overall system performance.
By carefully considering these factors, users can ensure they select a slip ring that can meet the unique needs of their radar antenna systems while providing reliable, high-performance operation across a wide range of conditions.
Conclusion
The conclusion will encapsulate the central themes discussed, reiterating the critical importance of the right slip ring in radar antenna systems and summarizing the aspects that determine their effective application in the field.
FAQs about Slip Ring Application in Radar Antennas
When it comes to integrating slip rings into radar antenna systems, several common questions arise about their selection, maintenance, and usage. Below we address these frequently asked questions to help users understand the critical aspects and best practices for deploying slip rings in radar applications.
Q1: How do I determine the correct size and configuration of a slip ring for my radar antenna?
A1: The size and configuration of a slip ring for radar applications depend on a variety of factors, such as the spatial limitations of your installation, the electrical and data transmission requirements, and the mechanical compatibility with the rotating part of the antenna. To determine the appropriate size and configuration, evaluate the mounting space available, the estimated power and signal channels needed, and the antenna’s rotation speed. Consulting with slip ring manufacturers to provide these details can lead to a tailored solution that fits your specific radar antenna requirements.
Q2: What kind of slip ring should I use for a radar system in a marine environment?
A2: For marine radar systems, it is important to choose a slip ring that offers robust protection against corrosion, water ingress (with appropriate IP rating), and potentially other factors like salt fog, high humidity, and wind. Materials like stainless steel and specialized coatings are preferred, and the design should seal electrical components effectively. Discussing with manufacturers about certifications for marine use is also recommended.
Q3: How often do slip rings need to be maintained in a typical radar antenna system?
A3: The frequency of maintenance for slip rings in radar systems varies depending on the operational environment, usage intensity, and design of the slip ring. For most applications, a periodic inspection is recommended at least once a year to ensure that wear and tear have not impacted performance. Nonetheless, some slip rings are designed to be maintenance-free for an extended period, especially those with advanced materials and design features that significantly reduce wear.
Q4: Can slip rings handle the high-frequency data transmission required by modern radar systems?
A4: Yes, many contemporary slip rings are capable of handling high-frequency data transmissions. Slip rings designed for this purpose often incorporate FORJs or other high-speed data transfer technologies. The key is to ensure that the slip ring specification matches or exceeds the frequency and bandwidth requirements of the radar system. It’s also important to consider proper EMI shielding to maintain data integrity.
Q5: What should I do if I observe data loss or signal interference in my radar system’s slip ring?
A5: If you notice data loss or signal interference in the slip ring of your radar system, first conduct a visual inspection for obvious signs of damage or wear. Check the electrical contacts and re they are clean and make proper contact. Consider whether environmental factors such as moisture or EMI could be affecting performance. Consulting with technical support from your slip ring supplier is also advisable to diagnose and resolve the issue.
Q6: Are there slip rings available that do not require physical contact to transmit signals and power?
A6: Yes, there are contactless slip rings, also known as “through-bore” or “capsule” slip rings, that use magnetic induction or other contactless technologies to transmit power and signals. These types of slip rings can be beneficial in reducing maintenance and improving the longevity of the unit by minimizing wear and tear.
Q7: How does temperature affect slip ring performance, and how can I mitigate any negative effects?
A7: Extreme temperatures can affect slip ring performance by causing expansion or contraction of materials, potentially leading to connection issues or mechanical failure. To mitigate these effects, it’s important to choose a slip ring rated for the operational temperature range of the radar system’s environment. Materials that have stable characteristics over a wide temperature range, like certain plastics or ceramics, can be used in the design to minimize temperature-induced problems.
See What We Can Do