As our understanding of mechanical systems and electrical engineering has progressed, specific devices have emerged as quintessential to our modern industrial landscape. Among these, slip ring systems, also known as rotary electrical interfaces, rotary joints, or rotary electrical couplings, stand out as remarkable and intricate innovations.
In its most basic sense, a slip ring system is a device that enables the transmission of power and electrical signals from a stationary unit to a rotating unit. The primary characteristic that renders them so fascinating is their capability to maintain an electrical connection amidst continuous rotation. This makes slip ring systems not just an accessory, but a vital component in the wider tapestry of numerous mechanical systems.
Across a multitude of applications – from making routine household appliances run smoothly, to allowing wind turbines to generate electricity, or enabling pivotal components in life-saving medical machines – slip ring systems play vital roles, often unseen and unappreciated by many of us. These formidable devices lend themselves to a large gamut of industrial applications, underscoring their relevance in today’s progressively automated and electrically driven world.
Whether in ensuring the optimal functioning of the high-speed trains or satellite systems, or lending their prowess to renewable energy sources, slip ring systems unassumingly yet competently fulfill their roles. As we embark on this detailed exploration of slip ring systems, it is essential to appreciate their underpinning importance in ensuring our access to numerous modern conveniences and vital services we often take for granted.
Operation and Constitutions of Slip Ring Systems
To truly grasp the value and prowess of slip ring systems, we must delve into their operational principles and constituent components. Their overall functioning, though layered and nuanced, rests on the foundational principle of creating an electrical connection between the static and the rotating parts of machinery.
At its core, a slip ring system functions based on two key shifts. Firstly, the electricity or signal coming from the stationary part of the device is converted into a form conducive for transmission, which then rotates along with the rotating part. Secondly, a reverse conversion happens where the transmitted power or signal is then converted back to its original form while maintaining the connectivity. This precise operation allows power or signals to cross this rotational interface, ensuring continued operation without hampering the rotation it caters to.
Diving into the constituents of a slip ring system, it essentially comprises a ring and a brush. The ring, generally made of conductive material, is aligned with the rotation and carries the electricity or signal. The brush, on the other hand, remains stationary and maintains an ongoing connection with the rotating ring, thus ensuring the purposeful transfer of power and signals.
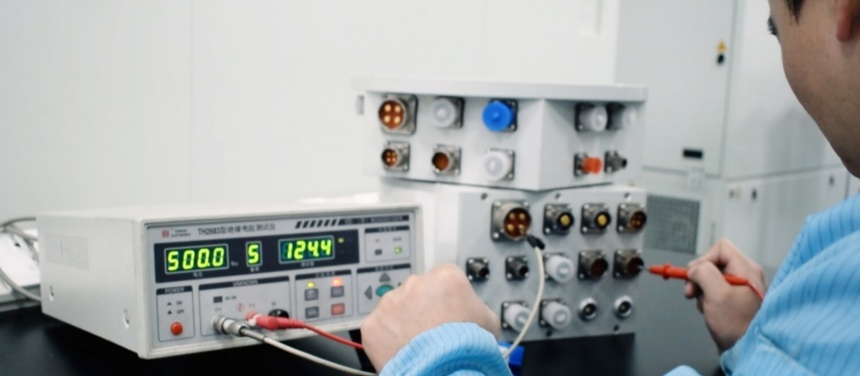
In more complex slip ring systems, additional components such as bearings, housings or cases, insulation materials, and more come into play. These are meticulously designed and assembled to withstand the challenges of different environments where they’re deployed — whether it’s a breezy wind turbine field or the intense depths of a mining site.
Bearings are crucial as they facilitate the smooth rotation of the slip ring assembly within the stationary part. The housing or the case protects the sensitive parts of the system from external factors, enhancing their durability and performance. The insulation material shields the system from potential dangers like short circuits or electrical faults.
In essence, the heart of a slip ring system’s operation lies in its ability to sustain an electrical connection amidst continuous rotation. Every component serves a unique role to achieve this delicate balance, resulting in this remarkable mechanical marvel.
Types of Slip Ring Systems
Just as biodiversity is crucial in the natural world, diversity in slip ring systems is fundamental to their applicability across a broad spectrum of industrial landscapes. Given the various demands and requirements posed by different devices and machinery, slip ring systems brightly become a driving force given their capacity to adapt and specialize.
Classification of the slip ring systems can be carried out based on a range of parameters, including their design, functionality, application, the kind of data or power they transmit, and the number of circuits they facilitate. This leads to several types of slip ring systems, each with their own unique set of characteristics and applicability.
Capsule slip rings, for instance, are compact in size, making them suitable for applications where space is a constraint. Contrarily, through-bore slip rings or hollow shaft slip rings come with a central hole, thereby providing the freedom to pass through mechanisms like shafts, making them ideal for operations involving hydraulic or pneumatic rotations.
In the case of pancake slip rings, the focus shifts to height reduction, with all elements being aligned on a single plane. This is particularly useful for applications where length is not a limiting factor, but space in terms of height is a constraint.
Mercury slip rings, on the other hand, employ a very different conductive medium – mercury. The use of liquid mercury, while posing handling challenges, vastly improves conductivity, reduces noise, and decreases wear and tear, making these slip rings exceptionally useful in scenarios where data integrity and reliability are crucial.
Finally, the future seems to tilt toward wireless slip rings or inductive slip rings, which follows the principle of electromagnetic induction and does not require any physical connection between the stationary and rotating parts. Though their usage is currently limited due to relatively lower power transmission capabilities, they hold significant potential for future applications.
In essence, the diverse world of slip ring systems is filled with specialized solutions for varied industrial requirements, emphasizing their adaptability and relevance.
Applications of Slip Ring Systems in Different Industries
The widespread applicability of slip ring systems across industries mirrors their ability to bridge the gap between stationary and rotating components, delivering uninterrupted electrical connections. Indeed, these devices lend themselves to numerous roles in a multitude of sectors, each time adapting and excelling at their given tasks.
Here are some notable instances where slip ring systems shine as pivotal components:
One of the most recognizable large-scale applications of slip ring systems is in wind energy generation. As wind turbines rotate to harness the kinetic energy of air, slip rings contribute by transmitting electricity generated by the turbine’s generator to the stationary grid system without hindrance.
Rotary tables
Industrial manufacturing often necessitates the use of rotational platforms for assembly work or test systems. In such cases, slip ring systems ensure the seamless transfer of electrical signals, power or even data between stationary control systems and the rotating platforms.
Aerospace and aviation equipment
From de-icing systems on aircraft wings to cutting-edge satellite technology, slip ring systems play an indispensable role in the realm of aerospace and aviation. These devices facilitate the transmission of crucial data, signals, and power to maintain the operational efficiency of these systems while enduring harsh environments.
Fill out our inquiry form to get the best price on slip rings.
CCTV and surveillance systems
In our increasingly security-conscious world, the importance of slip ring systems in closed-circuit television (CCTV) and surveillance systems is paramount. Utilized in sophisticated pan-tilt-zoom (PTZ) cameras, they enable the seamless transmission of video and control signals, allowing the devices to rotate without obstructing functionality.
The healthcare industry greatly benefits from the precise functioning of slip ring systems in life-critical devices like CT scanners and MRI machines. Ensuring interrupted power and data transfer as core components rotate, these systems guarantee accurate, reliable diagnoses to save lives.
Beyond these specific applications, slip ring systems find a place in numerous other industries including automotive, defense, entertainment, and telecommunications, to name a few. The breadth of their utility stems from their ability to adapt and evolve with technological advancements, ensuring an optimal match between the ever-changing landscape of human ingenuity and the devices we construct to meet our needs.
Challenges and Limitations of Slip Ring Systems
While slip ring systems are, no doubt, incredible pieces of engineering that bolster a multitude of industrial operations, it’s vital to acknowledge their inherent limitations and challenges.
Wear and Tear Due to Friction: Since the operation of a slip ring system involves mechanical contact between its various components, wear and tear due to friction is inevitable. This degrades the system over time, leading to efficiency loss and eventual replacement needs.
Environmental Constraints: The reliability and performance of slip ring systems can be heavily influenced by the environment in which they operate. Extremes of temperature, humidity, dust, and other environmental factors can have severe impacts on their lifespan and operational integrity.
Lifespan Limitation: Despite the best design and manufacturing practices, slip ring systems – like all mechanical devices – have a limited lifespan. The continuous rotation wears down components gradually, eventually necessitating maintenance or replacement.
High-Speed Operation Limitation: Slip ring systems might encounter limitations during high-speed operations. As the sliding speed increases, the friction and subsequent heat generation also rise. This can shorten the lifetime of contact materials and possibly lead to interruptions in signal or power transmission.
Noise and Signal Interference Issues: Due to inherent mechanical friction and electrical noise, slip ring systems might impose challenges to maintain the integrity of the signal, especially in sensitive instrumentation or communication applications.
These challenges serve as guideposts for future improvement and iterations in designing slip ring systems, pushing the technology to become more robust and adept in handling diverse scenarios. Simultaneously, they remind us to approach the deployment of these systems in an informed manner, considering the operational circumstances and maintaining them appropriately to maximize their utility.
User Concerns Regarding Slip Ring Systems
When contemplating the introduction or continuation of slip ring systems in their operations, users often grapple with various concerns. Understanding these concerns and identifying solutions is pivotal to harnessing the maximum potential of these systems.
Durability: The durability of slip ring systems rests on how well they cope with wear and tear, which potentiate concerns. Investing in quality systems equipped with adequate protection against mechanical and electrical strain can alleviate these concerns.
Efficiency: Concerns about the efficiency of slip ring systems, particularly their ability to transmit signals without degradation, often arise. It’s crucial to choose systems designed for the specific type of signals meant to be transmitted – be it power, data, video, or others.
Cost: The costs of procuring, installing, and maintaining a slip ring system can be a daunting prospect for users. However, viewing this as a strategic long-term investment rather than a short-term expense can dramatically shift this perception, considering the value and functionality they bring to operations.
Customizability: Given the uniqueness of different applications, users may worry about the ability to customize slip ring systems to their specific needs. Collaborating with manufacturers that offer customizable solutions, from the size and configuration to the number of circuits and types of signal transmission, can help overcome these concerns. For instance, an ID 7-inch slip ring can be tailored to accommodate specific requirements, such as handling larger currents, higher voltages, or a greater number of circuits for complex systems. This flexibility ensures that users can select the ideal slip ring for their application, whether it’s for robotics, industrial equipment, or other specialized machinery. The ability to customize the slip ring means that it can be optimized to meet the precise needs of the system, providing reliable performance and ensuring seamless integration into the overall design.
Maintenance: The necessity of regular maintenance to ensure optimal performance can also be a source of worry. Thankfully, many modern slip ring systems are designed with minimal maintenance needs. Furthermore, periodic maintenance and inspections can prolong the lifespan of these systems, leading to cost savings over the long run.
The concerns surrounding slip ring systems are undoubtedly valid. Nevertheless, by mindful selection, strategic planning, and ongoing maintenance, these systems can deliver excellent value over the long run. In numerous contexts, from high-end technology sectors to foundational industrial operations, their undeniable benefit continues to justify their widespread use.
Slip Ring Systems: Importance of Proper Care and Maintenance
Like any piece of machinery, the functionality, efficiency, and operational lifespan of slip ring systems significantly depend on their care and maintenance regimen. Proper maintenance not only aids in ensuring peak performance but also helps prevent unexpected breakdowns and failures.
Here is a comprehensive guide to help understand the aspects of an effective maintenance plan:
Regular Inspections: Conducting regular visual inspections allows for the timely detection of problems like wear and tear or potential mechanical issues. This facilitates preemptive measures, preventing minor inconveniences from escalating into major operational hitches.
Cleaning: Over time, debris or dust can accumulate on the slip rings and adversely impact performance. Regular cleaning with a soft cloth or brush can mitigate this. However, do note that the use of cleaning agents should adhere to the manufacturer’s recommendations to avoid any possible damage.
Lubrication: To ensure smooth functioning and reduce friction-induced wear, lubrication becomes essential. Ensure that you use the correct type of lubricant and follow the recommended lubrication schedule.
Insulation Checks: Insulation resistance tests should be performed on a bi-annual or annual basis, with results logged for performance tracking. Changes in insulation resistance could hint at potential issues that might need further investigation.
Professional Help: While preventive maintenance can be done in-house, it is advisable to seek professional help for remedial measures in the event of failures or breakdowns. Service providers typically possess the requisite experience and specific tools to diagnose and rectify issues effectively.
Above all, adherence to the manufacturer’s maintenance guidelines is essential. These guidelines take into consideration the specific design and construction details of the slip ring system, thereby providing the most reliable source of information for its care and upkeep.
Ensuring the longevity and operational integrity of slip ring systems necessitates a two-pronged approach – preventive in the form of regular care and purported in the form of professional maintenance when required. Undertaking these steps can significantly enhance their performance, reliability, and lifespan, thereby amplifying the returns on the investment made in these systems.
Future Prospects and Trends in Slip Ring Systems
As the industrial landscape continues to evolve, slip ring systems are also undergoing transformations to adapt and meet emerging demands. The future prospects and trends of these systems lie in the interplay of several factors, as outlined below:
Advancements in Material Science: From the development of wear-resistant materials to the exploration of self-lubricating ones, innovation in material science is set to significantly impact the design and longevity of slip ring systems. These advancements will enhance the efficiency and sustainability of these systems, transforming their usage across industries.
Seamless Integration with Digital Technology: As industries transition to Industry 4.0, slip ring systems must effectively integrate with digital technology. This could mean intelligent systems capable of real-time performance analysis, predictive maintenance, or seamless incorporation with IoT technology to boost operational efficiency.
Innovations to Reduce Maintenance: As we move forward, reducing maintenance needs without compromising system functionality is a clear trend. This might be achieved through improved design techniques, self-diagnostic capabilities, and the implementation of more wear-resistant materials to prolong the life of these systems.
Sustainable Production Practices: In an era of heightened environmental awareness, sustainable production practices are becoming increasingly significant. Future slip ring systems might be constructed from environmentally friendly materials, incorporating energy-efficient designs, or include features promoting recyclability or end-of-life management.
Customization as a Response to Diverse Needs: Given the wide array of requirements across different industries, the ability to customize slip ring systems will likely gain momentum. This includes bespoke designs to accommodate specialized transmission needs, unique configurations, or application-specific resistance to environmental factors.
In context, the future of slip ring systems is poised to be guided by these developments, leading to more sophisticated, reliable, efficient, and sustainable models. As these systems adapt to meet diverse needs, their role within different industries will not only persist, but it will also undoubtedly continue to evolve. The integral and dynamic nature of their functionality ensures their continued relevance for the foreseeable future.
Conclusion
Whether in terms of operation, application, or trends, slip ring systems form a fascinating section of mechanical engineering. As we continue evolving technologically, these systems are poised to meet and exceed our expectations, reinforcing their importance in modern machinery.
See What We Can Do