Welcome to our comprehensive guide on contactless slip rings. As our world becomes more technologically advanced, various systems and mechanisms evolve to support this growth. Contactless slip rings are one such innovation. In this guide, we endeavor to provide you with an all-encompassing understanding of contactless slip rings.
Providing an intricate blend of historical background, insights on key features, comparison among varied types, application scenarios, advantages, and much more, we aim to leave no stone unturned. For those eager to understand the technical matrix, we delve into the major components and their operational mechanism. Beyond the technical aspects, your understanding of the installation, maintenance, and common troubleshooting tips will be enhanced.
With the knowledge accumulated, you’ll be more equipped to understand the applications and opportunities in different industries as we walk you through some real-world examples. Finally, we bring you updated information on the latest advancements, market trends, and future prospects in the world of non contact slip rings.
Whether you’re an industry professional seeking more knowledge, a student exploring new topics, or someone considering the use of contactless slip rings in your business model, this guide is tailored just for you.
What are Contactless Slip Rings?
Definition and Explanation
Contactless slip rings, also known as wireless slip rings or non-contact slip rings, are electromechanical devices designed to transfer electrical power and data signals between a stationary and a rotating component without any physical contact. By leveraging advanced technologies such as inductive coupling, capacitive coupling, or radiofrequency-based transmission, contactless slip rings enable smooth and efficient power and signal transmission without the wear, noise, or friction associated with traditional slip rings.
These devices typically consist of two parts: a stationary component called the stator and a rotating component called the rotor. The stator and the rotor are designed to wirelessly transfer power and signals across a small gap, eliminating the need for brushes, which wear out over time in traditional slip ring designs.
The Significance and General Overview
Contactless slip rings have gained prominence due to their ability to overcome several limitations of traditional slip rings. By eliminating the physical contact between the stator and the rotor, contactless slip rings greatly reduce friction, wear, and tear, and noise during operation. They also provide improved performance in terms of low torque, increased longevity, and the capacity to transmit high-volume data and high-power signals with minimal interference.
The significance of contactless slip rings lies in their extensive application across various industries, including aerospace, defense, renewable energy (e.g., wind turbines), robotics, medical equipment (e.g., MRI machines), and telecommunications (e.g., rotating antennas in radar systems). By offering a maintenance-free solution, contactless slip rings help ensure high-quality, reliable, and disturbance-free data transmission and power transfer in these vital applications.
Their ability to perform seamlessly in harsh environments sets them apart from traditional slip rings. As they are not affected by factors like vibration, corrosion, dust, moisture, or extreme temperatures, contactless slip rings have become critical components in numerous systems requiring consistent and reliable performance.
In summary, contactless slip rings hold immense significance due to their superior attributes and applications, which have made them an indispensable part of various industries and critical systems. By providing enhanced efficiency, performance, and reliability, contactless slip rings are shaping the future of power and data transmission technologies.
History of Contactless Slip Rings
Evolution from Traditional Slip Rings to Contactless Slip Rings
The history of slip rings dates back to the early days of electrical engineering, where they were created to provide electrical connections between the stationary and rotating components of various systems. Traditional slip rings consist of brushes and commutators that maintain physical contact during the transmission of power and signals. However, the presence of brushes in these slip rings leads to several drawbacks, including wear and tear, noise, friction, and reduced life expectancy. This consequently results in lower performance and efficiency, as well as higher maintenance costs.
As technology progressed, the need for a more efficient and reliable mode of transmission became evident. Researchers and engineers sought ways to overcome the limitations of traditional slip rings, leading to the development and eventual emergence of contactless slip rings. By using electromagnetic principles and advanced wireless communication techniques such as inductive coupling, capacitive coupling, or radiofrequency transmission, contactless slip rings addressed the drawbacks of their traditional counterparts.
The invention of contactless slip rings has led to significant improvements in various fields. With no physical contact between the stator and the rotor, contactless slip rings have successfully eliminated issues of wear and tear, friction, and noise, resulting in extended life spans and reduced maintenance needs, all while providing improved performance and efficiency across diverse applications.
Key Advancements & Innovations
Numerous advancements and innovations have taken place in the field of contactless slip rings. Some of the key developments and breakthroughs include:
- Development of wireless transmission technologies: The invention of different wireless transmission techniques, such as inductive coupling, capacitive coupling, and radio frequency transmission, has played a crucial role in the growth of contactless slip rings. Each of these technologies brings unique advantages, making contactless slip rings suitable for various applications.
- Miniaturization: Technological improvements have led to the development of compact and lightweight contactless slip rings, enabling their integration into a wider range of systems with minimal space requirements. The reduction in size has allowed contactless slip rings to be used in smaller devices with demanding size constraints, such as drones, medical equipment, and sensors.
- High-performance materials and components: The use of advanced materials, such as high-temperature-resistant and corrosion-resistant materials, contributes to enhanced performance and increased compatibility with diverse environments. Additionally, improvements in semiconductor technology have boosted the efficiency and speed of data transmission in contactless slip rings.
- Multi-channel and high-speed data transmission: As wireless communication technology has evolved, contactless slip rings have been adapted to accommodate multi-channel and high-speed data transmission capabilities. These innovations have allowed industries to benefit from more reliable and seamless communication, even in demanding applications.
These advancements and innovations have paved the way for the expanded use of contactless slip rings, enabling them to play an increasingly important role in numerous critical applications across various industries.
Contactless Slip Rings Prospect
The prospect for contactless slip rings is promising due to their unique advantages and the growing demand in various high-tech and demanding applications. Here are some key aspects of their future prospects:
Technological Advancements
- Increased Performance: Continued advancements in materials and technology are likely to improve performance, allowing for even higher speeds, greater reliability, and broader temperature ranges.
- Miniaturization: Ongoing efforts to reduce size and weight will make contactless slip rings suitable for increasingly compact and portable devices.
Growing Applications
- Medical Technology: The need for high-precision, high-reliability components in medical imaging and diagnostic equipment is likely to drive demand.
- Aerospace and Defense: As aerospace and defense systems become more complex, the demand for durable, low-maintenance components will grow.
- Industrial Automation: With the rise of automation and robotics, especially in harsh environments, contactless slip rings will become more prevalent.
Enhanced Capabilities
- High-Speed Data Transmission: The need for faster and more reliable data transmission in applications like telecommunications and data centers will boost the demand for advanced contactless slip rings.
- Integration with Smart Technologies: Integration with IoT and smart technologies will expand their use in various high-tech and automated systems.
Market Expansion
- Emerging Markets: As technology spreads to emerging markets, there will be increased opportunities for contactless slip rings in new industries and applications.
- Increased Adoption: Adoption in sectors like renewable energy (e.g., wind turbines) and automotive (e.g., electric vehicles) will likely increase.
Environmental Considerations
- Sustainability: The trend towards environmentally friendly and sustainable technologies could drive the development of more eco-friendly materials and manufacturing processes for contactless slip rings.
Customization and Flexibility
- Tailored Solutions: The ability to customize contactless slip rings for specific applications will cater to a wide range of industries and requirements, enhancing their versatility.
Overall, the contactless slip ring market is expected to grow as industries demand more advanced, reliable, and efficient components to meet evolving technological and performance needs.
Features of Contactless Slip Rings
Key Features and Technical
Contactless slip rings come with several key features that differentiate them from their traditional counterparts. Here are some notable ones:
- Non-contact transmission: Unlike traditional slip rings, contactless slip rings transmit power and data without any physical connection between the stationary and rotating components. This eliminates mechanical friction and wear, resulting in a longer operating life and minimal maintenance.
- High-frequency response: Contactless slip rings offer a broad frequency response range and can support high-speed data and signal transmission.
- High reliability and performance: Due to the absence of brushes and mechanical wear, contactless slip rings provide high reliability and stable performance over an extended period of time.
- Environmentally resistant: These devices exhibit superior performance in challenging environmental conditions, including high and low temperatures, high humidity, dust, and vibration.
- Integration capabilities: Contactless slip rings can be easily integrated into various systems owing to their compact design and flexible installation options.
Unique Features of Different Types
Depending on the transmission method used, contactless slip rings fall into different categories, each offering unique features:
- Inductive coupling slip rings: These slip rings transfer electrical power magnetically through inductive coupling which reduces electromagnetic interference. They are widely used in applications that require a moderate amount of power transmission with low data rate requirements.
- Capacitive coupling slip rings: These types of contactless slip rings transfer power and signals via the electric field between high-frequency electrodes. They are known for their ability to transfer high volumes of data at fast speeds, but they typically support lower power transmission.
- Radiofrequency (RF) slip rings: RF rotary joints, or rotary joints, are designed to transmit radio frequency signals. They offer high-speed and high-capacity data transmission, making them an excellent choice for telecommunications, radar systems, satellite dishes, and other data-intensive applications.
These unique features enable designers to choose the most suitable type of contactless slip ring based on the specific needs and constraints of their project.
Contactless Slip Rings Specifications
Contactless slip rings have specific specifications tailored to their applications and requirements. Here are some common specifications you might encounter:
Electrical Specifications
- Voltage Rating: Typical ranges from 5V to 1000V or more, depending on the application.
- Current Rating: Ranges from a few milliamperes to several amperes per channel.
- Signal Types: Can handle various signal types including analog, digital, RF, and high-speed data.
Mechanical Specifications
- Rotation Speed: Capable of handling high rotational speed, often up to several thousand RPM.
- Rotation Angle: Usually supports continuous 360-degree rotation.
- Dimensions: Varies based on application; custom sizes can be manufactured to fit specific needs.
Environmental Specifications
- Temperature Range: Can operate in a wide temperature range, typically from -40°C to +85°C.
- Protection Rating: Often rated for IP65 or higher, ensuring protection against dust and water ingress.
- Durability: Designed for long-term operation with minimal maintenance, often with lifespans extending beyond several million revolutions.
Performance Specifications
- Signal Integrity: Maintains signal quality with minimal attenuation and noise, ensuring high-fidelity data transmission.
- Electrical Noise: Low electromagnetic interference (EMI) to prevent signal disruption.
- Reliability: High reliability with built-in redundancy and fail-safes in critical applications.
Mechanical Design
- Mounting Options: Can be designed for various mounting configurations, such as flange, through-hole, or custom mounts.
- Connector Types: Various connectors can be used based on application requirements, including custom and standard connectors.
Other Features
- Data Transfer Rate: Capable of handling high-speed data transfer rates, which can vary based on application requirements.
- Customizability: Often customizable to meet specific needs, including number of channels, signal types, and physical dimensions.
These specifications ensure that contactless slip rings can be used effectively in a range of demanding applications, from industrial machinery to aerospace systems.
Types of Contactless Slip Rings
Inductive Slip Rings
Inductive slip rings use the principles of electromagnetic induction for power and data transmission. They consist of two inductively coupled coils placed close to each other—one in the rotating component and the other in the stationary component. As the power is applied, a magnetic field is generated in the stationary coil, which induces an electric current in the rotating coil, thereby transferring the power or signals. Inductive slip rings are best suited for moderate power transmission and lower data rate requirements in environments where contact and wear could be problematic, such as underwater or high-speed rotating applications.
Radio Frequency (RF) Slip Rings
RF slip rings, or rotary joints, are used for transferring high-frequency signals across a rotating interface, thanks to the principles of electromagnetic wave propagation. They are crucial in systems such as radar antennas, satellite communication systems, or medical imaging equipment, where they enable the transmission of high-speed and high-capacity data without interference. RF slip rings can handle a broad range of frequencies, including microwave-level frequencies, making them indispensable for modern, high-bandwidth applications.
Capacitive Slip Rings
Capacitive slip rings transmit power and signals using the electric field between high-frequency electrodes. They are essentially a type of capacitive coupling that allows power and signal transfer across a small, non-conductive gap, providing excellent performance in high-speed, high-data-volume applications. While capacitive slip rings typically support lower power transmission compared to other types, they excel in environments that prioritize fast, high-volume data transmission over power needs.
Comparisons and Usage Scenarios
Inductive, Radio Frequency, and Capacitive slip rings each have unique strengths and are utilized in different usage scenarios.
- Inductive Slip Rings are often used in moderate power transfer applications where the device might be exposed to adverse conditions such as continuous rotation, high-speed operation, or damp and underwater environments. Examples include wind turbines, marine equipment, and high-speed cameras.
- Radio Frequency Slip Rings shine in scenarios requiring the transmission of high-speed and high-capacity data. They are commonly seen in communication systems such as radar and satellite communication, where high-bandwidth data transmission is mandatory.
- Capacitive Slip Rings excel in high-speed data transfer scenarios and are commonly used in applications like digital video transmission, high-speed automation, optical communication, and medical devices which require high-quality, reliable, and fast data transmission.
Therefore, the selection between inductive, RF, or capacitive slip rings depends on the specific needs of the device or system, such as power requirements, data transmission speed, environmental factors, and available space.
Need a custom slip ring solution? Contact us by filling out the form.
Components and How They Work
Major Components of Contactless Slip Rings
The primary components of contactless slip rings include the transmitter, the receiver, and the control circuitry.
- Transmitter: The transmitter is situated on the stationary side of the system (also known as the stator). Its purpose is to convert the input power and signals into the appropriate form (magnetic fields for inductive slip rings, high-frequency electric fields for capacitive slip rings, and radio signals for RF slip rings) for wireless transmission.
- Receiver: The receiver is positioned on the rotating side of the system (popularly known as the rotor). It takes the transmitted magnetic or electric fields or radio signals, converting them back into electrical power and signals that can be used by the rotating device or component.
- Control Circuitry: The control circuitry plays a vital role in managing the operation of the slip ring. It controls the transmitter’s frequency and signal strength to ensure smooth and reliable power and signal transmission. It also regulates the receiver to facilitate accurate and efficient converting of the fields or signals back into usable power and data.
Detailed Operation Mechanism
The operation of a contactless slip ring can be broken down into several steps:
- Power and signal input: The first step involves providing the power and signals to the transmitter side of the slip ring. This energy and information can come from various sources, such as a power supply or a control system.
- Conversion and transmission: The transmitter then processes the power and signals and converts them into a suitable form for transmission. For instance, inductive slip rings generate a magnetic field, capacitive slip rings create a high-frequency electric field, and RF slip rings produce radio signals. This converted form of power and signals is then transmitted across the gap between the stationary and rotating parts.
- Reception and conversion: The receiver on the rotating side accepts the transmitted magnetic field, electric field, or radio signals and converts them back into electrical power and signals. This process ensures the power and signals can be used by the rotating system or device.
- Utilization: Finally, the electrical power and signals received and processed by the receiver are sent to whatever device or component on the rotating side needs them.
This transmission process ensures a continuous and reliable supply of power and signals across the stationary and rotating parts of a system, effectively enabling several key functions and applications in today’s world.
Benefits of Contactless Slip Rings
Advantages Of Traditional Slip Rings
Contactless slip rings offer several compelling advantages over traditional slip rings, including:
- Extended Life and Reduced Maintenance: Without the physical brush and commutator connections that contribute to wear and tear, contactless slip rings have a significantly longer operational life and require less maintenance, yielding reduced downtime and overall lower lifecycle costs.
- No Contact Noise: Contactless slip rings eliminate the problem of contact noise that traditional slip rings endure due to their brush-commutator interface. This factor is particularly important in systems requiring stable and noise-free transmission.
- Higher Speeds: Given that there’s no physical contact, these slip rings can handle higher rotating speeds, paving the way for use in more demanding applications.
- Improved Data Transmission: Contactless slip rings are capable of supporting the transmission of more complex signals (including high-frequency and data signals) with exceptional clarity and minimal loss, an attribute not always achievable with traditional slip rings.
- Greater Environmental Compatibility: Being brushless makes contactless slip rings less prone to problems related to dust, dampness, or corrosive environments, which can severely affect the performance of traditional slip rings.
Specific Benefits in Different Application Scenarios
In different applications, the benefits of contactless slip rings are particularly pronounced:
- In the industrial automation field: Contactless slip rings can operate at high speeds without the risk of wear, providing reliable and uninterrupted power and signal transmission. This feature enables more efficient, accurate, and smooth automation processes, leading to productivity and cost savings.
- In wind energy systems: These slip rings withstand harsh environmental conditions and require minimal maintenance, qualities needed in wind turbines where high altitude, rotation speed, weather conditions, and maintenance accessibility are prominent challenges.
- In medical imaging devices: Contactless slip rings outperform in transmitting complex and high-volume data signals without interference, a critical requirement in medical imaging machinery such as CT and MRI machines.
- In communication systems and satellites: With their high-frequency response and ability to handle large data volumes, RF slip rings are crucial in these systems for ensuring clear, reliable, and fast communication.
In summary, contactless slip rings not only outperform traditional slip rings but also provide specialized benefits in various applications, making them a prime choice for myriad modern industries and technologies.
Uses of Contactless Slip Rings
Contactless slip rings, also known as non-contact slip rings or contactless rotary joints, offer several advantages due to their design that eliminates physical contact between rotating and stationary parts. Here are some of their key uses:
- High-Speed Rotations: Ideal for applications requiring high rotational speeds, as they reduce wear and tear associated with contact-based slip rings.
- Harsh Environments: Used in environments with extreme temperatures, dust, or moisture where traditional slip rings might fail due to wear or contamination.
- Medical Equipment: Common in MRI machines and other medical devices where avoiding physical contact is crucial for maintaining high image quality and preventing interference.
- Aerospace: Employed in spacecraft and aircraft where reliability and minimal maintenance are essential. They are used in satellite antennas and avionics systems.
- Robotics: Found in robotic arms and other automated machinery to ensure reliable power and data transfer without mechanical wear.
- Telecommunications: Used in rotating antennas and communication systems where uninterrupted signal transmission is required.
- Defense: Utilized in military systems and equipment for secure and reliable data transmission in rotational applications.
- Industrial Automation: Applied in rotating machinery and equipment in manufacturing processes where durability and minimal maintenance are important.
- Cameras and Surveillance: Employed in pan-tilt-zoom cameras and surveillance systems to ensure smooth rotation and uninterrupted video feed.
- Wind Turbines: Used in the nacelle of wind turbines for transmitting power and data between the rotating blades and the stationary base.
By eliminating friction and wear, contactless slip rings offer enhanced longevity and reliability in demanding applications.
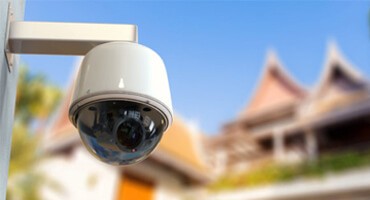
Surveillance Video
Applications and Industries of Contactless Slip Rings
Key Industries Where Contactless Slip Rings are Used
Several key industries and applications have leveraged the benefits of contactless slip rings:
- Renewable Energy Industry: In particular, wind turbines widely use contactless slip rings to convey electrical signals and power between the stationary tower and the rotating blades.
- Telecommunication Industry: RF slip rings are indispensable for transferring a vast amount of data in radar systems and satellite equipment, ensuring reliable communication.
- Medical Industry: Contactless slip rings are critical components in advanced medical imaging equipment (e.g., CT and MRI machines), where they facilitate the transmission of high-quality images and data.
- Defense & Aerospace: In focus-intensive applications such as target acquisition systems, remote weapons stations, and unmanned aerial vehicles (UAVs), contactless slip rings provide much-needed reliability and accuracy.
- Industrial Automation: The continuous and flawless transmission of power and signals within rotating parts of automated machinery is made possible by the employment of contactless slip rings.
Real-World Application Examples
Practical applications highlight the immense versatility and functionality of contactless slip rings:
- Wind Turbines: Within a wind turbine, the blades’ rotational motion is used to generate power. Contactless slip rings transfer this power from the revolving generator to the stationary electrical grid, overcoming the problem of constant rotation without any wiring issues.
- CT Scanners: In a CT scanner, the X-ray tube and detectors rotate around the patient to capture detailed images from various angles. Contactless slip rings here provide power and data communication between the rotating and stationary parts without impeding the scanner’s motion.
- Satellite Communication Systems: RF slip rings in satellite communication antennas allow the antenna to rotate continuously, receiving and sending data signals without interruption. This ensures reliable communication, a critical factor in timely weather updates, global positioning services, or telecommunication.
- Industrial Robots: In automated manufacturing processes, robots need to execute their tasks without power or signal interruptions. Therefore, contactless slip rings are implemented to facilitate the smooth operation of these rotating robotic parts.
Contactless slip rings, therefore, have a broad range of practical applications, showcasing their instrumental role in improving the functionality and efficiency of devices across multiple industries.
Contactless Slip Rings Installation and Maintenance
Installation Process
The installation process for contactless slip rings may vary depending on the specific type and model, but the general steps include:
- Checking Compatibility: Before installation, it’s crucial to ensure the slip ring is compatible with the system in terms of size, power rating, signal types, and operating conditions.
- Positioning: Once compatibility is confirmed, the next step is to position the slip ring properly. It should be installed in a location where the fixed (stator) and moving (rotor) parts match the structure of the device or machine.
- Mounting: Proceed to mount the slip ring securely. For most slip rings, this involves attaching the stator to the stationary component of the application and the rotor to the rotating part. Ensuring a secure fit is important to prevent any unwanted movement that could affect the slip ring’s operation.
- Wiring: Connect the power and signal sources to the correct terminals of the slip ring. Following the manufacturer’s wiring diagram or instructions is crucial at this stage to prevent any errors.
- Testing: Finally, upon successful installation, a series of tests should be carried out before full operation to confirm that the slip ring is working as expected and no issues are present.
Maintenance and Troubleshooting Tips
Being contactless, these slip rings require less maintenance than their traditional counterparts. However, to ensure their optimal functioning and prolonged life, some basic maintenance and troubleshooting steps should be followed:
- Regular Checks: Perform regular visual checks for any signs of physical damage or loose connections that might need attention.
- Cleanliness: Keep the installation area clean. Although contactless slip rings are inherently less affected by dust or debris, maintaining cleanliness can still contribute to their overall longevity and reliability.
- Listen for Noise: If any unusual noises are heard during operation, they may indicate a problem. A qualified service technician should be summoned to inspect the system if this occurs.
- Respecting Operating Conditions: Ensure that the slip ring’s operating conditions, such as temperature, humidity, speed, and load, are within the specified limits to prevent premature failure or performance issues.
Effective installation and maintenance practices are the key to ensuring the longevity and reliable performance of contactless slip rings.
Current Developments and Future Prospects
Latest Advancements
The contactless slip rings industry continues to evolve, driven by ongoing technological advancements:
- Enhanced Materials: Much interest has been shown in the use of advanced materials to improve the efficiency of energy transmission in these slip rings. For instance, the use of cutting-edge semiconductor materials has led to better power conversion efficiency and broader frequency range capabilities.
- Miniaturization: As in many fields of technology, there’s a growing emphasis on making contactless slip rings smaller, lighter, and more cost-effective without compromising performance. Miniaturized models are especially valuable in applications where space is a constraint, such as drones or small robotic systems.
- Integrated Systems: Another noticeable trend is the development of integrated slip rings that bundle power transmission, signal transmission, and other capabilities into a single module. This type of integrated system simplifies system design and installation, leading to cost-saving and reduced complexity.
Market and Future Trends
Looking ahead, the contactless slip ring market is anticipated to grow significantly driven by several trends:
- Green Energy Expansion: With the global shift toward renewable energy, the demand for contactless slip rings, particularly in wind turbines, is set to increase.
- Growth in Automation: Increased reliance on automation across industries, from manufacturing to food processing, is expected to boost the demand for contactless slip rings as they are crucial for power and signal transmission in automated machinery.
- Advancements in Communication Technologies: As 5G and beyond networks roll out in the coming years, advanced contactless RF slip rings capable of supporting high-frequency, high-data-volume transmissions will be increasingly sought after.
Through leveraging these technological advancements and keeping pace with the upcoming market trends, there is the promising growth potential for the contactless slip ring industry. In essence, continuous advancements in materials, design, and integration capabilities alongside growing demands in renewable energies, increase in automation, and improvements in communication technologies are set to drive the development and applications of contactless slip rings to new heights.
Have specific slip ring requirements? Submit your inquiry here.
Conclusion
Contactless Slip Rings have revolutionized the transmission of power and signals between stationary and rotating parts. They alleviate the issues experienced with traditional slip rings by offering superior reliability, efficiency, and longevity. As industries continue to embrace digital transformation, the future promises an even broader range of applications and developments for contactless slip rings.
FAQs about Contactless Slip Rings
As contactless slip rings play an integral role in numerous applications, it is valuable to gain a deep understanding of their functionality and characteristics. Here are some frequently asked questions and their answers to help clarify further:
Q: How do Contactless Slip rings work?
A: Contactless slip rings work using the principles of wireless power transmission, primarily electromagnetic induction or capacitive coupling. They consist of a rotor and a stator that are in close proximity but do not physically touch. The signals or power from the static part (stator) are transferred wirelessly across the air gap to the rotating part (rotor).
Q: What are the Advantages of Contactless Slip Rings Over Contact Slip Rings?
A: Contactless slip rings offer several benefits over their traditional contact counterparts. They include a higher degree of reliability, longevity, and less maintenance due to the lack of physical wear and tear, better signal quality, the ability to operate at higher speeds and greater resistance to challenging environmental conditions.
Q: What Industries Use Contactless Slip Rings?
A: Various industries use contactless slip rings, such as wind energy production (wind turbines), telecommunications (satellite systems and radars), medical industry (CT and MRI scanners), defense & aerospace (unmanned aerial vehicles, radar systems), and industrial automation (robotic units).
Q: What Factors to Consider During Installation?
A: First, ensure compatibility with your system to prevent any potential issues. Then, place the slip ring where the moving and stationary parts align with the device’s structure. Secure the slip ring and then proceed with the wiring. After installation, conduct testing to ensure everything works properly. Always follow the manufacturer’s instructions or consult professionals during the installation process to avoid complications.
Q: Are Contactless Slip Rings Maintenance-free?
A: While contactless slip rings require far less maintenance than contact slip rings due to no physical wear, some light upkeep such as ensuring cleanliness, checking for physical damage or loose connections, listening for abnormal noises, and operating within the product specifications is recommended to prolong their service life and functionality.
Understanding these FAQs can shed light on the fundamental principles, advantages, applications, and technical aspects of contactless slip rings, enabling users to make informed decisions and handle these vital components effectively.
See What We Can Do