In the realm of electromechanical devices, low-current slip rings hold a distinctive place. These components, although often overlooked, play a vital role in various applications, significantly contributing to technological advancements. This comprehensive guide aims to unravel the intricacies of low-current slip rings, highlighting their importance, operational mechanisms, application domains, and potential future trends.
Introduction to Low-Current Slip Rings
Low-current slip Rings are a specialized class within the broader family of slip rings, an integral component in numerous electromechanical devices. These rings operate on the principle of maintaining an electrical connection between a stationary and a rotating part of a mechanism. As their name suggests, these slip rings are specifically designed to handle low electrical currents without causing significant power loss or signal interference.
Low-Current Slip Rings are compact in design, and owing to the nature of their operation, they exhibit minimal electrical noise levels and optimal conductivity, even in demanding environments. The internal parts are typically made of high-quality, conductive material, offering resilience and enhanced durability. Construction variations are quite versatile, considering the vast range of applications, leading to different sizes, materials, and designs to meet specific application requirements.
The importance and role of Low-Current Slip Rings extend to a myriad of technological applications. Their primary function is in devices that need to transmit power or data signals without interruption from a stationary entity to a rotating component without breaking the connection. For instance, rotating tables, surveillance systems, wind turbines, industrial machinery, medical equipment, and even radar antenna are commonplace examples where these rings are used.
In these applications, Low-Current Slip Rings contribute vastly to the efficient and effective operation of the system by enabling uninterrupted power or signal transmission even during rotation. Their design allows for minimal signal loss, and lower heat generation, and thereby helps to ensure that the systems run smoother and more reliably. As we continue to rely more on evolving technologies and communication systems, it becomes even more important to understand and appreciate the role of these foundational components.
This article will provide a comprehensive understanding of Low-Current Slip Rings, considering aspects like their working mechanism, construction and material considerations, and noteworthy application areas. By delving into these facets, readers will gain a deeper understanding of these essential yet relatively overlooked components, helping them appreciate the critical role they play in many of the technological conveniences we enjoy today.
Have a Low-Current Slip Rings inquiry? Get a quick response here.
The Working Mechanism of Low-Current Slip Rings
Before delving into the particulars of low-current slip rings, it’s essential to understand the foundational operational principles of slip rings at large. In its most fundamental form, any slip ring serves as an electromechanical device that allows for the transmission of electrical power or signals from a stationary to a rotating part. At the core of this process are two key components: the conductive ring and brushes. As the ring rotates, usually attached to the rotating component, the brushes maintain consistent contact with the rings, ensuring a continuous electrical connection.
This basic mechanism remains the same for all varieties of slip rings, including both high and low current variants. However, low-current slip rings deviate in their design and operation to aptly handle the demands of managing lower electrical currents. Several design variations and adaptations play a crucial role in enabling low-current slip rings to offer seamless electrical communication in a diverse range of primarily smaller, precision-oriented applications.
Contrarily, high-current slip rings are built larger and designed to carry greater electrical currents through systems like turbines or heavy industrial machinery. Their design, often more robust, accommodates a more significant heat generation due to the higher current flow, necessitating better heat dissipation characteristics in comparison to their low-current counterparts.
On the other hand, low-current slip rings are crafted to minimize friction, resistance, and heat generation, as these factors are more influential in systems with lower current magnitudes. They employ highly conductive materials, optimized brush designs, and superior wear-resistant technologies to ensure a consistent, reliable flow of lower currents or signals. This key distinction in the design approach centers around the premise of ensuring smooth operation with minimal power or signal interruption, while also enhancing lifespan and performance efficiency, which is a critical aspect for applications that demand precision and consistency.
By delving into the working mechanisms of low-current slip rings, we can better appreciate their critical role in maintaining the smooth operation of various components across several technological sectors.
Materials and Construction of Low-Current Slip Rings
Typical Materials Used
The choice of material plays a crucial role in determining the performance characteristics of low-current slip rings. While materials like copper and silver alloys are widely used in slip ring assemblies for their excellent electrical conductivity properties, low-current slip rings often employ enhancements such as gold plating to improve contacts, ensuring a reduction in signal noise and better wear resistance. This is particularly helpful in fine electrical instrumentation and communication applications where even the smallest amount of noise or signal degradation can have significant implications.
Influence of Material Choice
The selection of material for low-current slip rings directly influences their performance characteristics in various ways, as highlighted below:
- Conductivity: Efficient electrical signal transmission hinges on the conductivity of the chosen material. Copper and silver alloys are popular choices for their exceptional electrical conductivity, facilitating seamless low-current operation.
- Durability: The durability of any mechanical or electrical component is inherently tied to its construction material. As low-current slip rings often operate in settings demanding precision and consistency, the use of high-quality materials is essential in ensuring extended, reliable performance.
- Wear Resistance: The material used in the construction of low-current slip rings greatly influences its wear resistance. By incorporating elements such as gold plating on contact surfaces, the slip ring achieves greater wear resistance, directly translating to a longer service life while minimizing disruptions caused by worn-out parts.
Design and Construction Elements
To enable low-current operation, the design and construction of low-current slip rings prioritize specific factors:
- Smaller and More Precise Connections: Low-current operation necessitates small, precise connections to prevent power leakage or cross-talk between channels. The design of these slip rings ensures that components are carefully arranged and sized, with narrow gaps and close tolerances.
- Optimized Brush Design: The brushes used in low-current slip rings are often fine-tuned to minimize friction and resistance. Some designs employ specially shaped brushes or incorporate precious metal fibers (such as gold) to enhance performance efficiency while mitigating wear and tear.
- Temperature and Environmental Protection: Low-current slip rings are designed to maintain stable performance despite varying environmental conditions. Appropriate sealing technologies and protective enclosures are employed to shield the device from dust, moisture, or other potential contaminants, ensuring the consistency of low-current operation.
By selecting the right materials, employing strategic construction techniques, and catering to the unique demands of low-current applications, the performance and efficacy of low-current slip rings can be significantly enhanced. It is this careful attention to detail and design optimization that ensures these small yet vital components can play their essential role in a multitude of industries and technologies.
Applications of Low-Current Slip Rings
Low-current slip rings find their utility in a vast array of applications, primarily where precision, consistency, and seamless rotation are prerequisites. Their small size, low electrical noise, and high wear resistance make these slip rings ideal components for numerous miniature devices, precision instrumentation, and data communication systems. Below, we explore some of these applications in greater detail:
Precision Instrumentation
Precision devices, ranging from medical tools such as rotary catheters, and endoscopes, to index tables in manufacturing or research microscopes, greatly benefit from low-current slip rings. Their rotation-friendly design allows for seamless movement and uninterrupted data or power transfer, serving as a pivotal link between the stationary and rotating parts of these instruments. Importantly, their low-noise operation and high signal fidelity ensure accurate and reliable results, which is essential for precision-oriented applications.
Miniature Devices
Miniaturization is a key trend in many sectors, and the electronics industry is no different. From tiny surveillance cameras to high-speed EDM machines, these compact devices rely on low-current slip rings to maintain consistent electrical contact despite continuous rotation. The small design of these slip rings allows them to fit into tight spaces, making them an indispensable part of numerous miniature devices.
Data Communication Systems
Data communication systems rely heavily on uninterrupted, clear signal transmission. Low-current slip rings find application in radar installations and satellite communication systems, where they facilitate the rotation of antennae while maintaining a constant connection. Their exceptional signal integrity and low electrical noise ensure that vital data is transferred accurately, contributing significantly to the overall system efficiency.
Industrial Automation & Robotics
Industrial robots often need to make multi-axis movements while transmitting signals and power to their various tooling systems. Low-current slip rings allow these complex movements by providing a continuous electrical connection between the rotating parts and the control system, all while ensuring minimal signal distortion and electrical noise.
To conclude, these are just a handful of the multitude of applications that low-current slip rings cater to. The versatility of these devices, coupled with their robust design and superior performance traits, make them an integral component across several technological and industrial sectors.
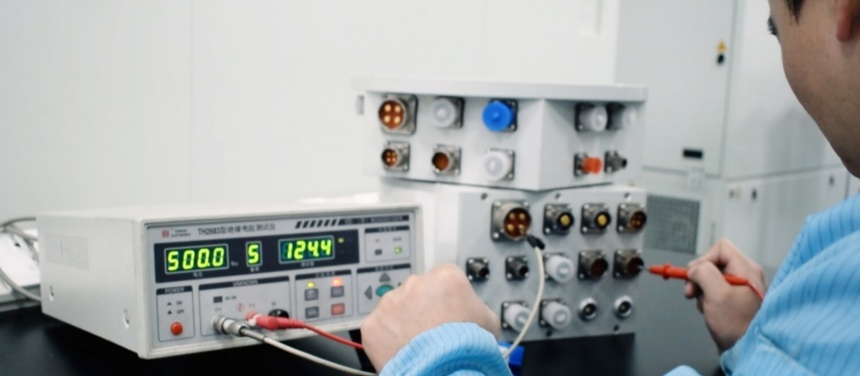
Important Factors to Consider When Choosing a Low-Current Slip Ring
Selecting the right low-current slip ring is pivotal to the performance of the overall system in which it is embedded. Since it is a piece of the puzzle that directly facilitates essential functions like power or signal transfer, careful consideration should be employed while making a selection. Here are key factors to consider:
Electrical and Mechanical Performance Parameters
Understanding the electrical and mechanical requirements of your system is the first step in choosing the right slip ring. These requirements often include specifications for operating current or voltage, switching capabilities, rotational speed, maximum temperature tolerance, etc. For example, if your system requires handling moderate power transmission, a 15A 400V slip ring might be an ideal choice. This slip ring is designed to operate efficiently with 15 amps of current and a voltage of up to 400V, ensuring it meets the power demands of your system. Additionally, the 15A 400V slip ring is engineered to handle specific rotational speeds and temperature variations, making it suitable for a range of applications, including industrial machinery, robotics, and more. Understanding these needs ensures that the chosen slip ring is equipped to handle the specific parameters it will need to operate within, providing reliable performance and longevity.
Compatibility with the Specific System
Not all low-current slip rings are made equal. Different models are designed to meet specific needs. Therefore, understanding the characteristics of the system in which the slip ring will be implemented is crucial. For instance, the ring’s physical dimensions, the amount of electrical noise it may produce, and even the number of channels it can handle should align with the system’s requirements to ensure a seamless fit.
Durability and Materials Used
The longevity of the slip ring is often directly tied to the quality of the materials used in it. Look for devices that employ durable, high-conductivity materials that promise longevity against wear and tear. Additionally, features such as gold-plated contacts or high-impact plastic housing can also contribute to extending the ring’s operational lifespan.
Certifications and Standards
Ensure that the slip ring is manufactured according to appropriate industrial or international standards. Such certifications are a testament to the slip ring’s reliability and can ensure that it’s built to meet precise technical requirements. Common certifications may include ISO 9001 for quality management or CE certification for European standards, among others.
In conclusion, the task of selecting a suitable low-current slip ring is a critical one, involving careful consideration of various aspects of the device’s design and specifications. By following these guidelines, the chances of selecting a slip ring that ensures efficient operation and long-term reliability will be significantly increased.
Maintenance and Care of Low-Current Slip Rings
Proper maintenance and care of low-current slip rings are critical to their longevity and efficient operation. These devices facilitate the continual transmission of electrical signals or power, and their reliability directly impacts the performance of the systems they’re a part of. The following are some key tips and practices for ensuring the care and longevity of low-current slip rings:
Ensuring Longevity
- Regular Lubrication: Proper lubrication reduces friction and wear between the rotating ring and the brush contacts. Use a lubricant recommended by the manufacturer to prevent unnecessary wear and tear, which can prolong the life of the slip ring.
- Careful Operation: Avoid operating the slip ring beyond its specified mechanical and electrical limits. Overloading or improper use can lead to accelerated wear or even catastrophic failure.
- Proper Installation: Correct installation, according to the manufacturer’s guidelines, helps prevent potential mechanical stresses, ensuring optimal operation and longevity of the slip ring.
Regular Inspection and Cleaning
- Inspection Cycles: Regular inspection of the slip rings for signs of wear or damage can help in the ly detection of problems, thereby preventing complete failures. Set up a routine inspection cycle as suggested by the manufacturer, as the frequency can vary based on the slip ring’s operating conditions.
- Cleaning: Over time, contaminants can accumulate on the surface of the slip ring, disrupting the electrical contacts and causing noise or signal loss. Regular cleaning, using approved solvents or materials, can keep the contact surfaces clean and contribute to better performance.
- Part Replacement: If wear or damage is detected during an inspection, it is crucial to replace the damaged components with manufacturer-approved parts to prevent further issues.
By following a rigorous maintenance routine and taking proactive measures in the care of low-current slip rings, operators can ensure the longevity and reliability of these vital components. Remember, a well-maintained slip ring not only provides reliable service but also contributes to the efficiency and productivity of the wider system in which it operates.
Latest Innovations and Future Trends in Low-Current Slip Rings
As technology evolves, so does the demand for better-performing low-current slip rings. Over the years, manufacturers and researchers have focused on improving the efficiency, longevity, and utility of these components to cater to the needs of increasingly advanced applications. In this section, we take a closer look at some of the recent innovations in low-current slip ring design and the potential trends that could steer this domain in the future.
Recent Technological Advancements
- Contactless Slip Rings: One notable innovation is the development of contactless slip rings that use electromagnetic or optical coupling to transmit power and signals. These designs eradicate mechanical wear and significantly reduce electrical noise, offering a promising alternative to traditional slip rings.
- Integrated Sensors and Encoders: Modern slip rings incorporate various advanced sensors and encoders that allow the system to monitor operational performance and health. These integrated diagnostics help in predicting maintenance schedules, reducing the risk of unforeseen failures, and improving overall efficiency.
- High-Performance Brush Materials: Ongoing research in brush design and materials has led to the utilization of precious metal fibers and advanced composites, which simultaneously reduce friction, wear on the rings, and electrical noise. These innovations contribute to better-performing slip rings that can operate for longer periods without maintenance.
Potential Future Applications and Trends
- Internet of Things (IoT) and Industry 4.0: With the rise of IoT and Industry 4.0, there will be an increased demand for slip rings that can facilitate efficient data transfer, low latency, and high-speed operation. Innovations catering to these requirements will continue to be developed, as these high-performance slip rings become essential components of increasingly interconnected systems.
- Renewable Energy Applications: The global push for renewable energy sources continues to steer novel applications for slip rings. For instance, they’re expected to play a crucial role in wind turbine generators, where their reliable performance under harsh weather conditions and the ability to transfer power and data seamlessly will be essential.
- Space and Defense Technologies: As space exploration and defense technologies advance, the need for low-current slip rings that can operate in extreme conditions will grow. The development of slip rings that can withstand variations in temperatures, frictionless operation in vacuum environments, and radiation-resistant designs will be prioritized in this domain.
The future of low-current slip rings will be driven by emerging technologies and their accompanying applications. By pushing the boundaries of innovation and embracing the latest advancements, the low-current slip ring industry will continue to evolve, supporting, and enabling the rapid growth of numerous sectors that depend on these vital components.
Conclusion
In summary, low-current slip rings, although small in size and scale, carry enormous significance in various technological domains. Understanding their working mechanism, applications, and maintenance can ensure their effective usage, contributing to more efficient and reliable systems. As we march forward, these humble components are likely to be at the heart of future innovations, powering the world one rotation at a time.
FAQs about Low-Current Slip Rings
Low-current slip rings are complex devices often used in sophisticated applications, from precision instrumentation to industrial automation. They connect stationary and rotating parts of a mechanism allowing the transfer of power and electrical signals. Here, we address some of the common queries prospective users or the public may have about these vital components:
Q: What is a low-current slip ring?
A: A low-current slip ring is a specialized electrical connector designed to transmit power and electrical signals from a stationary part of a device to a rotating part. These slip rings are optimized for lower current levels, typically used in precision instruments or miniature devices where compactness, reduced electrical noise, and seamless rotation are essential.
Q: How long can a low-current slip ring last?
A: The lifespan of a low-current slip ring depends on various factors such as the quality of materials used, operating environment, load conditions, and maintenance practices. With appropriate care and under optimal conditions, some low-current slip rings can last for millions of revolutions or several years of operation.
Q: Can a low-current slip ring transmit data?
A: Yes, besides power, low-current slip rings can also transmit electrical signals, including data. They are often used in devices like radar systems, where they enable the rotation of the antenna while maintaining continuous data flow.
Q: How are low-current slip rings maintained?
A: Maintenance for low-current slip rings typically involves regular inspections for wear and damage, cleaning to remove contaminants, and lubrication to reduce friction. Certain models may also require part replacements as part of their maintenance routine. Users should always refer to the manufacturer’s guidance for maintenance best practices.
Q: Do all low-current slip rings produce electrical noise?
A: While all low-current slip rings will produce some degree of electrical noise due to their working mechanism, the exact level can vary significantly. Contactless slip rings, for example, reduce this noise to a minimum. Design components, such as gold contacts or advanced brush materials, can also help minimize electrical noise.
See What We Can Do