As integral parts of rotating systems utilized in several modern industries, magnetic slip rings play a pivotal role. This article demystifies the concept of magnetic slip rings, showcasing their functionality, benefits, and applications, and sheds light on user concerns.
Introduction to Magnetic Slip Rings
A magnetic slip ring serves as a crucial electromechanical component that facilitates the effortless transmission of electrical signals and power between a stationary system and a rotating part. Essentially, it bridges the gap between the moving and static components of a larger device, ensuring that vital power and information flow remain continuous and uninterrupted.
Magnetic slip rings are vastly utilized across various industries, from renewable energy applications such as wind turbines to military devices like radar systems. Understandably, the demand for these versatile components has surged in tandem with the escalating adoption of rotating equipment worldwide.
The primary function and purpose of magnetic slip rings revolve around their ability to reliably maintain electrical connectivity, even amidst constant motion. They significantly reduce wear and tear on the components, as well as friction and heat generation, due to their contactless nature, which is based on electromagnetic induction. The result is a smooth, uninterrupted flow of critical data and power supply, optimizing the performance of any device in which they are integrated.
In short, magnetic slip rings serve as a linchpin for many industrial applications by delivering high-quality, dependable connectivity solutions for power and data across rotating systems. As technology advances and industries grow, the importance of these devices cannot be overstated—they ensure seamless communication, optimized performance, and a reduced need for maintenance, all of which contribute to enhancing the scope and potential of devices that rely on them.
Components of a Magnetic Slip Ring
A magnetic slip ring comprises several vital components that work in a synchronized manner to aid and maintain unfaltering electrical connections, while the herculean task of transmitting signals and power between stationary and rotating parts ensues. The harmonized functionality of these components underpins the overall success and reliability of the magnetic slip ring. Let’s delve a bit into these primary components and their correlated function.
The main parts of a magnetic slip ring include the rotor and stator, which represent the core of the device’s functionality. The rotor, aptly named due to its rotational feature, typically connects to the moving part of the device. Conversely, the stator stays stationary, anchoring to the non-moving part. The intricate dance between the rotor and stator forms the essence of the magnetic slip ring, as they maintain the dynamic energy and signal transmission.
Another important set of components in the magnetic slip ring system is the electrically conductive brushes and rings. However, contrary to traditional mechanical slip rings that create a physical connection between these components, magnetic slip rings operate on the principle of magnetic coupling in place of direct contact. This attribute significantly reduces wear and tear, thus prolonging the life span of these components.
The aforementioned set-up functions using magnetic fields. When the rotor spins, it creates a magnetic field which, through electromagnetic induction, produces a current in the stator. No physical contact is necessary in this process, reducing friction and subsequent heat generation.
In essence, each component of the magnetic slip ring plays a cardinal role, ensuring smooth, uninterrupted transmission of power and electrical signals. From the rotor’s rotation and the stator’s stasis to the magnetic coupling that replaces physical wear, every part works in symphony to uphold efficiency and durability that embody the magnetic slip rings in the industrial world.
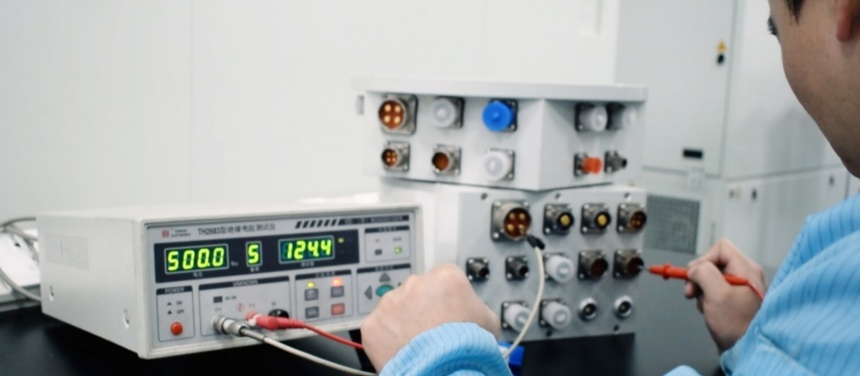
Function and Operation of Magnetic Slip Rings
To truly appreciate the relevance and impact of magnetic slip rings on a plethora of industrial equipment, it’s essential to detail their function and operational principles. Despite their seemingly complex functionality, magnetic slip rings operate on an elegant and straightforward principle known as electromagnetic induction, a concept first discovered by physicist Michael Faraday.
At its core, a magnetic slip ring functions by transmitting power and electrical signals through magnetic fields from a stationary unit (stator) to a rotating unit (rotor) within an equipment. This aids in the continuous operation of the device without the need for wired connections that often restrict movement or risk disconnection.
Let’s break down the operational process: the rotor, being attached to the rotating part of the machine, spins at a speed paralleled with the device. As the rotor spins, in virtue of its integrated magnets, it generates a changing magnetic field. This magnetic field penetrates through the air gap between the rotor and stator (the stationary part). The magnetic field induces electric currents within the stator, this process embodies the principle of electromagnetic induction.
The beauty of this process lies in its contactless nature. Unlike traditional mechanical slip rings that rely on physical connections (such as brushes) to transmit signals and power, magnetic slip rings do this wirelessly. This crucial feature safeguards the device from potential physical wear and tear, friction, and heat generation that could otherwise impair functioning and reduce the lifespan of the device.
Hence, the fundamental operation of magnetic slip rings emphasizes exploiting the principles of electromagnetic induction to enable the contactless transmission of power and electrical signals. This elegant operation sustains the uninterrupted functionality of the device and significantly contributes to its longevity and efficaciousness.
Types of Magnetic Slip Rings
In the world of electromechanical devices, there is a magnetic slip ring tailored to suit just about every type of application. The variations typically emerge from differing requirements in terms of circuit numbers, current ratings, operating speed, and housing protection levels, among others. With these variations come a wide range of applications.
Firstly, let’s address circuit numbers. Some applications only require a few circuits for transmitting power or signals, while others need a higher number. A standard magnetic slip ring can come with as few as one or two circuits and extend to dozens, depending on the specific application it serves.
Secondly, different devices demand different current ratings. For instance, some delicate applications may need a low-current slip ring, while heavy machinery or high-power equipment might require slip rings rated for high current. This high versus low current rating is another critical factor guiding the selection of magnetic slip rings.
Next is the operating speed – magnetic slip rings’ novelty lies in their ability to function well at high speeds due to the absence of friction from contact. Some types are designed for low-speed operations, while others are engineered for high-speed applications, such as high-speed trains and aerospace devices, rendering a broad spectrum of options.
Additionally, the level of housing protection plays a pivotal role. Many industries operate under harsh conditions, where slip rings are exposed to dust, moisture, and other corrosive elements. Some magnetic slip rings are housed in protective coverings to guard the components within and ensure uninterrupted functioning of the slip ring despite challenging environments.
Lastly, it is important to note that there are also specialized types of magnetic slip rings for unique applications. These include Ethernet slip rings for Ethernet signal transmission, wind turbine slip rings for renewable energy applications, and even capsule slip rings for compact devices.
In conclusion, the diverse range of magnetic slip rings is a testament to their adaptability and flexibility. Each type is designed with specific applications and industries in mind, thus ensuring that they perfectly suit the varying demands of the electromechanical world.
Benefits of Using Magnetic Slip Rings
Magnetic slip rings are often the unsung heroes in various industries, from renewable energy to automation, medical devices to aerospace, imparting their unique characteristics to enhance the efficiency and durability of systems. They come with distinct advantages that make them a preferential choice in many applications, and their benefits are manifold.
One of the most remarkable benefits of magnetic slip rings is their reduction of wear and tear. Traditional mechanical slip rings work on physical contact between brushes and rings, which causes friction and subsequently leads to gradual wear over time. Magnetic slip rings, on the other hand, make use of magnetic fields to create contactless communication between the rotating and stationary parts. This significantly reduces physical wear and tear, increases the lifespan of the slip ring, and ensures consistent performance.
Longevity is another impressive attribute of magnetic slip rings. Owing to the minimized friction during operation, these slip rings tend to have prolonged service life. This, together with their robust construction, makes magnetic slip rings a highly cost-effective option for various applications, reducing the total cost of ownership through decreased maintenance and replacement costs.
The third noteworthy benefit is their adaptability to high-speed rotations. Unlike their traditional counterparts, magnetic slip rings can maintain efficient transmission, even under high rotational speeds. This makes them suitable for applications needing high-speed operations and positions them as a go-to choice for advanced and high-demand industrial applications.
Lastly, their non-contact operation inherently reduces heat generation—a common issue with traditional slip rings. This allows magnetic slip rings to operate at lower temperatures, enhancing their performance and durability while ensuring safety in a heat-sensitive environment.
In conclusion, the benefits of using magnetic slip rings are unequivocal. Their contactless nature which results in less wear and tear, their longevity, adaptability to high-speed rotation, and reduced heat generation collectively make magnetic slip rings an excellent choice for industries seeking the balance between performance, durability, and cost-effectiveness.
Applications of Magnetic Slip Rings
Magnetic slip rings have found their way into a plethora of industries and applications, a testament to their versatility, efficiency, and reliability as critical electromechanical devices. They are well-suited when contactless transmission of power and electrical signals is paramount. Here, we will explore some of the key industries and applications where magnetic slip rings shine, as well as offer specific examples and case studies illustrating their practical implementation.
Industries and Applications
- Renewable Energy: Wind turbines rely on magnetic slip rings to convey power and data between the fixed tower and the rotating nacelle and blades, regardless of their rotational speed. This ensures consistent power generation and facilitates condition monitoring to optimize maintenance and reduce downtime.
- Medical Imaging: Magnetic slip rings are commonly used in medical imaging devices, such as CT scanners, where the rotation of X-ray detectors requires continuous power and signal transmission. Their minimal maintenance requirements and ability to perform at high speeds are vital in capturing detailed images and maintaining patient safety.
- Robotics and Automation: Highly automated systems and robotics frequently utilize magnetic slip rings to maintain uninterrupted communication and power supply as they rotate. Industrial robotics, both in manufacturing and warehousing facilities, rely on magnetic slip rings to instantly access power and control signals, resulting in a seamless workflow.
- Defense and Aerospace: Radar systems in both military and civil aviation require precision and continuous communication. The rotor and antenna array of radar systems depend on magnetic slip rings to maintain a constant flow of power and data from the stationary base to the rotating antennas.
- Entertainment and Amusement: Theme park rides, stage equipment, and lighting systems feature complex rotations and movements. Magnetic slip rings facilitate the execution of these dynamic feats by providing constant power and signal transmission between moving and stationary components.
Case Studies and Examples
Wind Turbine Slip Ring Application: In a wind turbine, the nacelle contains the generator and other crucial components, rotating to align with the wind. Signal transmission between the rotating nacelle and the stationary tower necessitates a reliable slip ring. Magnetic slip rings are preferred for their maintenance-free operation, longevity, and ability to work in harsh environments with fluctuating temperatures, humidity, and airborne salt particles.
CT Scanner Slip Ring Application: A Computed Tomography (CT) scanner consists of a stationary gantry and a rotating component, housing X-ray emitters and detectors. As the rotating part spins around the patient, it relies on magnetic slip rings for uninterrupted power and data transmission. The slip ring’s contactless operation minimizes moving parts, reducing maintenance needs and ensuring a smooth, high-speed operation critical to producing high-quality images.
In conclusion, the applications of magnetic slip rings span a wide array of industries and devices. From renewable energy to medical technology, their contactless transmission, reduced wear-and-tear, and versatility make them an indispensable tool in modern electromechanical systems.
Key Considerations When Choosing a Magnetic Slip Ring
The selection of an appropriate magnetic slip ring requires careful consideration of various factors to ensure compatibility, efficiency, and durability. Keeping in mind the specific application and environment in which the slip ring will operate, one has to analyze an assortment of elements, such as size, weight, compatibility, and cost.
Size and Weight
The size and weight of a magnetic slip ring are vital considerations, especially in limited-space or weight-sensitive applications. For compact devices, using smaller, capsule slip rings can be advantageous. However, reducing size may come at the cost of circuit number or current capacity. Finding the right balance is crucial to matching the specifications of the specific device or machinery.
Get in touch with our sales team by filling out the form below.
Current Rating
Different devices demand different current ratings, which directly correlate to their power transmission capabilities. It is essential to choose a slip ring that can comfortably handle the current levels required for the application. Low-current slip rings are suitable for delicate systems, while heavy machinery or high-power equipment necessitate high current ratings.
Operating Speed
Magnetic slip rings are particularly well-suited for high-speed applications, thanks to their contactless nature. However, depending on the application, the slip ring’s rotational speed might vary. One must verify that the chosen slip ring can handle the expected rotational speed, whether it’s low or high, to ensure smooth and uninterrupted power and signal transmission.
Environmental and Installation Compatibility
The operating environment affects the choice of magnetic slip rings significantly. Some applications, like wind turbines, demand slip rings with robust housing and protection from dust, moisture, or corrosive elements. Therefore, assessing the environmental conditions and ensuring compatibility is crucial for optimal performance and durability.
Communication and Signal Requirements
Some applications demand the transmission of specific types of signals or data, such as Ethernet or fiber optic. Ensuring that the chosen magnetic slip ring meets these communication requirements is essential for seamless operation. Clarifying the signatories beforehand allows for a better fit and smoother implementation of the slip ring.
Cost
Budgetary constraints are often critical in the decision-making process. While magnetic slip rings may have higher upfront costs than traditional mechanical slip rings, their longer lifespan, low maintenance, and reliable performance can offset the initial expenditure in the long run. Analyzing the total cost of ownership, including maintenance and replacement costs, will contribute to a more informed decision.
To sum up, choosing the right magnetic slip ring entails careful evaluation of various factors, such as size, weight, current rating, operating speed, environmental compatibility, communication requirements, and cost. Considering these aspects allows for the selection of a magnetic slip ring tailored to the specific needs of the application, ensuring seamless operation and overall system efficiency.
What Users Are Mostly Concerned About Magnetic Slip Rings
When integrating a magnetic slip ring into a device or system, users often have a range of concerns. These apprehensions are usually centered around aspects such as durability, functionality under varying conditions, maintenance needs, price, and more. Addressing these concerns is pivotal for informed decision-making.
Durability and Lifespan
One of the primary concerns is undoubtedly the durability and lifespan of the magnetic slip ring. Users often ponder over how long the device will last, especially considering their slightly higher upfront cost. Fortunately, due to their contactless operation, magnetic slip rings tend to have a longer lifespan and typically suffer less wear and tear compared to traditional mechanical slip rings.
Functionality Under Different Conditions
The functionality of magnetic slip rings under diverse environmental conditions is another common concern. Users with applications in hostile environments may worry about the slip ring’s ability to perform under high or low temperatures, fluctuating humidity levels, and exposure to dust or other corrosive elements. Luckily, many magnetic slip rings are packaged in robust, protective housings designed to withstand challenging environmental conditions.
Maintenance Needs
The need for regular maintenance and its associated costs often worry users. Maintenance involves not just monetary costs, but also operational downtime which could impact productivity and efficiency. Since magnetic slip rings have fewer moving parts and operate without physical contact, the need for regular maintenance is substantially reduced, which is a relief to many users.
Compatibility and Integration
Users might also have concerns regarding the compatibility of the magnetic slip ring with their existing systems and how easy it is to integrate them into their devices. Compatibility issues could lead to inefficiencies or malfunctions. Hence, it is crucial to carefully consider the slip ring’s specifications against the requirements of the application.
Price
Price is an ever-present consideration for any buyer. While magnetic slip rings can come with a higher price tag due to their advanced technology, the benefits they offer often justify this cost. Additionally, the reduced maintenance, improved durability, and extended lifespan often lead to lower long-term expenses.
Signal Integrity
Preserving signal integrity is a crucial aspect of applications that hinge on the seamless transmission of data or signals. Imperfections or disruptions in signal transmission can lead to inefficiencies or malfunctions. Users often enquire about the capabilities of the magnetic slip ring to preserve signal integrity.
In conclusion, while prospective users of magnetic slip rings might have a series of concerns, most of them are assuaged by the inherent advantages and adaptive capabilities of these devices. To ensure that these concerns are duly addressed, it is always beneficial to consult with the manufacturer or an informed source during the decision-making process.
Top Manufacturers of Magnetic Slip Rings
Prominent manufacturers in the industry include MOOG, Schleifring, and Hangzhou Grand Technology, each known for their quality products and innovative advances within the field.
No. | Manufacturer | Website |
---|---|---|
1 | Hangzhou Grand Technology | https://www.grandslipring.com/ |
2 | Moog Inc. | https://www.moog.com/ |
3 | Stemmann-Technik | https://www.stemmann.com/en/home |
4 | Schleifring | https://www.schleifring.com/ |
Hangzhou Grand Technology
Hangzhou Grand Technology Co., Ltd. started as a special slip ring manufacturer in 2011. Grown into slip rings, rotary joints, and slip ring assembly experts of today with 6,000 square meter manufacture complex.
Obtained ISO9001, Rosh, CE, and GJB9001B certificates a number of slip rings, rotary joint patents, and proud of our products can meet military grade. Collaborated with universities, institutes, and renowned factories across Asia and Europe including Panasonic, SIEMENS, CSIC, SAMSUNG, HUAWEI, etc.
Moog Inc.
Moog is a leading supplier of high-performance slip rings for various industries, including aerospace. Among their offerings, Moog’s SR Series Slip Rings are designed for the demanding environments of helicopters, excelling in performance, reliability, and customization potential.
Stemmann-Technik
Stemmann-Technik, a part of the Conductix-Wampfler Group, offers a broad range of slip rings, including solutions for helicopters. Their Livietta Slip Ring Assemblies are designed explicitly for harsh and demanding environments in the aviation sector, providing reliable signal and power transmission.
Schleifring
Schleifring is a well-known manufacturer of electromechanical systems, including slip rings customized for various industries. Their Aircraft Slip Rings cater specifically to helicopters, offering robust performance, low wear, and high reliability to meet the challenges of aviation applications.
If you want to know more about other slip ring manufacturers, you can read Top 10 Slip Ring Manufacturers in China, Top 10 Slip Ring Manufacturers In the USA Market 2023, and Top 10 Slip Ring Industry Key Manufacturers 2023.
Conclusion
Magnetic slip rings stand as indispensable pillars within multiple sectors, owing to their flexibility, durability, and their efficacy in facilitating uninterrupted transmission. Understanding their function, benefits, common concerns, and best practices in selection can lead to their optimal utilization, further driving advancements in the rotating equipment realm.
See What We Can Do